تكنولوجيا المطرقة الهوائية المتقدمة للهدم السريع
كفاءة غرفة الضغط المستمر
غرف الضغط الثابت في المكابس الهوائية تغير اللعبة حقًا عندما يتعلق الأمر بإنجاز أعمال الهدم بشكل أسرع. توفر الغرف قوة متواصلة طوال فترة التشغيل، وهو أمر تؤكده الأبحاث الصناعية بالأرقام، حيث تُظهر أداءً أفضل بنسبة 20٪ مقارنة بالأنظمة الهوائية الأقدم. ما الذي يجعل هذا ممكنًا؟ في الواقع، تدير الغرف تدفق الهواء بشكل أكثر ذكاءً، لذلك لا تضيع تلك الطاقة الثمينة هباءً. وتشير تقارير المقاولين إلى أنهم يوفرون المال على استهلاك الهواء أيضًا، مما يعني عمليات أكثر استدامة من الناحية البيئية. ميزة كبيرة أخرى هي أن هذه الغرف تدوم لفترة أطول بين فترات الصيانة. فهي مصممة لتتحمل الضغوط بشكل أفضل، لذلك لا تهترئ القطع بسرعة. وهذا يعني الحاجة إلى استبدال أقل على المدى الطويل. مع الحفاظ على ضغط ثابت طوال الوقت، يجد العمال أنفسهم يقضون وقتًا أقل في إصلاح الآلات، ويقضون وقتًا أكثر في تفكيك الأشياء بكفاءة.
أنظمة تسليم التأثير عالي التردد
المكابس الهوائية إن الأنظمة المزودة بتأثيرات عالية التردد تُعزز بالفعل من أداء الهدم وتُنجز العمل بشكل أسرع. وقد أفاد المقاولون بزيادة الإنتاجية بنسبة تصل إلى 25٪ في العديد من المواقع، مما يُظهر الفعالية الكبيرة لهذه الأدوات. ما يجعلها بهذا القدر من الجودة؟ إن طريقة عملها توفر قوة تكسير كبيرة في حين تُخفف من الجهد المبذول من قبل المشغل. ويعني الانخفاض في الارتداد أن العمال لا يشعرون بالإرهاق بسرعة خلال فترات العمل الطويلة، وهو أمر تؤكده التقارير الميدانية مرارًا وتكرارًا. لكن هذه الأنظمة ليست قوية فقط، بل إنها متعددة الاستخدامات أيضًا. سواء كان الأمر يتعلق بهدم طبقات سفلية من الخرسانة السميك أو إزالة دقيقة للأسطح دون إلحاق الضرر بالمناطق المحيطة، فهناك دائمًا إعداد للتأثير يناسب كل حالة. وتتيح هذه المرونة توفير المال، لأن الطواقم لا تحتاج إلى امتلاك أدوات متخصصة متعددة. ما عليك سوى تغيير الإعدادات والانتقال بسلاسة من مهمة إلى أخرى مباشرة.
التحسين الطاقي في عمليات الهدم
استراتيجيات تقليل استهلاك الهواء
شهد قطاع الهدم تغييرات كبيرة بفضل تقنيات التحكم في الهواء الجديدة التي جسّدت طريقة إدارة استهلاك الهواء في الموقع. ذكر بعض المشغلين أنهم قللوا استخدام الهواء بنسبة تصل إلى 30٪، مما يساعد البيئة في الوقت الذي يوفرون فيه المال. تفقدوا التقارير الميدانية الأخيرة من مواقع البناء في وسط الولايات الأمريكية - حيث شهد أحد المقاولين انخفاضًا كبيرًا في المصروفات الشهرية بعد تبديل الأنظمة. كما انخفضت فواتير الطاقة لدى عدة شركات عندما بدأوا باستخدام ممارسات أفضل لإدارة الهواء. تتوالى قصص النجاح. حيث نفّذت شركات مثل ABC Demolition وXYZ Contractors هذه الابتكارات وأظهرت نتائج حقيقية على صعيد تقليل التكاليف وخفض البصمة الكربونية مع مرور الوقت.
تشغيل أدوات مزدوجة من مضغوطات واحدة
تتيح إعدادات الأدوات المزدوجة للعمال تشغيل عدة مثقبات هوائية في وقت واحد من ضاغط هواء واحد فقط، مما يؤدي إلى استخدام أفضل للموارد بشكل عام. كما يوفر هذا الإعداد مساحة عمل قيمة في مواقع العمل، ويوفر مرونة أكبر لفرق الهدم عند العمل في أجزاء مختلفة من المشروع. على سبيل المثال، يمكن للمقاولين تشغيل مثقبات كبيرة على الجدران الخرسانية في حين تتعامل مثقبات أصغر مع الأنابيب القريبة وفي الوقت نفسه. تُظهر الخبرة العملية أن الشركات توفر المال على تكاليف التشغيل وأنجاز المزيد من العمل بسرعة بعد الانتقال إلى هذه التكوينات لأنظمة مزدوجة. وتجد الشركات التي تتعامل مع مشاريع هدم معقدة أنها تستطيع إنجاز الأعمال أسرع دون الحاجة إلى معدات إضافية متراكمة في الموقع، مما يجعل هذه الأنظمة عملية في الاستخدام اليومي وخيارات اقتصادية ذكية على المدى الطويل.
تصاميم إنسانية تُعزز إنتاجية المشغل
ابتكارات في مقابض خفض الاهتزاز
إن التصاميم الجديدة لمقبض المفكات الهوائية تحدث فرقاً حقيقياً عندما يتعلق الأمر بخفض الاهتزازات. هذا يعني أن العمال لا يشعرون بالإرهاق نفسه خلال فترات العمل الطويلة في مواقع العمل. لقد بدأ المصنعون باستخدام مركبات مطاطية خاصة وأنظمة داخلية لامتصاص الصدمات في مناطق المقبض لامتصاص كل تلك الحركات الاهتزازية التي كانت تنتقل عادةً عبر الذراع. نحن نتحدث عن عوامل تمنع مشاكل صحية خطيرة مثل متلازمة اهتزاز اليد والذراع وفقاً للمعهد الوطني للسلامة والصحة المهنية. العمال الذين انتقلوا إلى استخدام هذه الأدوات الحديثة يذكرون باستمرار أنهم يشعرون بتحسن حقيقي طوال يوم عملهم. بل ويقول البعض أنهم قادرون على البقاء منتجين لفترة أطول لأن أيديهم لم تعد تشعر بالخدر الناتج عن الاهتزازات المستمرة. إن هذا النوع من التحسينات لا يُعد مجرد ترف، بل هو مهم فعلاً لضمان سلامة الأشخاص أثناء إنجاز المهام بكفاءة.
البناء الخفيف لتقليل الإرهاق
أصبحت مثاقب الهواء الخفيفة تحسينًا كبيرًا في مجال الراحة الوظيفية، حيث تساعد في تقليل الأثر على أجسام العمال أثناء الورديات الطويلة. يبني المصنعون هذه الأدوات الآن باستخدام مواد مركبة متقدمة وخلائط معدنية خاصة تقلل الوزن مع الحفاظ على المتانة تحت الظروف القاسية. الوزن الأخف يعني إجهادًا أقل على الذراعين والظهر، مما يسمح للمشغلين بالعمل لفترة أطول قبل التعب. بعض النماذج الحديثة من المثاقب تزن فعليًا حوالي 20% أقل من الإصدارات الأثقل السابقة، لكنها لا تزال توفر نفس القوة عند كسر الخرسانة أو الأسفلت. يبقى من المهم إيجاد التوازن الأمثل بين خفة الوزن الكافية للتعامل معها طوال اليوم وبين القوة الكافية لأداء المهام الشاقة. تحقق العديد من العلامات التجارية المتاحة في السوق هذا التوازن بشكل جيد، مما يخلق أدوات لا تضحي بالأداء فقط لتوفير بعض الكيلوجرامات. عندما تستثمر الشركات في هذه الأدوات الأخف وزنًا، فإنها تلاحظ فوائد حقيقية من حيث رضا العمال والإنتاجية العامة في مواقع العمل على مدار الأسبوع.
هدم فعال باستخدام الكسارات المدمجة
المناورة في البيئات الحضرية الضيقة
تأتي الكسارات الصغيرة بمزايا خاصة تجعلها فعالة للغاية في التنقل داخل المساحات الحضرية المزدحمة، ولذلك فهي مفيدة جداً عند هدم المباني في حالات ضيق المساحات. إن تصميم هذه الآلات يسمح للعمال بإتمام المهام بسرعة مع ضمان حماية المباني والطبيعة المحيطة من أي أضرار. يشير العديد من العاملين في المشاريع الحضرية إلى سرعة إنجاز الأعمال عند استخدام الكسارات الصغيرة. على سبيل المثال، في إحدى الدراسات التي رأيناها الشهر الماضي، ذكر بعض المخططين البلديين أن الانتقال إلى النماذج الصغيرة قلل من مدة عمليات الهدم بنسبة تصل إلى الثلث مقارنة بالمعدات الأقدم والأكبر حجمًا.
إن النظر إلى المشاريع الفعلية يظهر بوضوح مدى كفاءة عمل هذه الآلات. خذ على سبيل المثال مشروع الهدم الأخير في مانهاتن السفلى حيث كانت المساحة ضيقة للغاية. كانت المكثفات الصغيرة ضرورية للغاية في هذا الموقع. تمكن العمال من الوصول إلى تلك الشوارع الجانبية الضيقة ومناطق البناء الصغيرة التي لا تستطيع المعدات العادية المرور فيها. سارت العملية برمتها بسلاسة أكثر مما كان متوقعاً، وظلت المتاجر القريبة مفتوحة معظم الوقت. تُحدث هذه المرونة كل الفرق في المدن المزدحمة حيث يُعد كل إنش مربع مهماً أثناء تنفيذ مشاريع البناء أو الهدم.
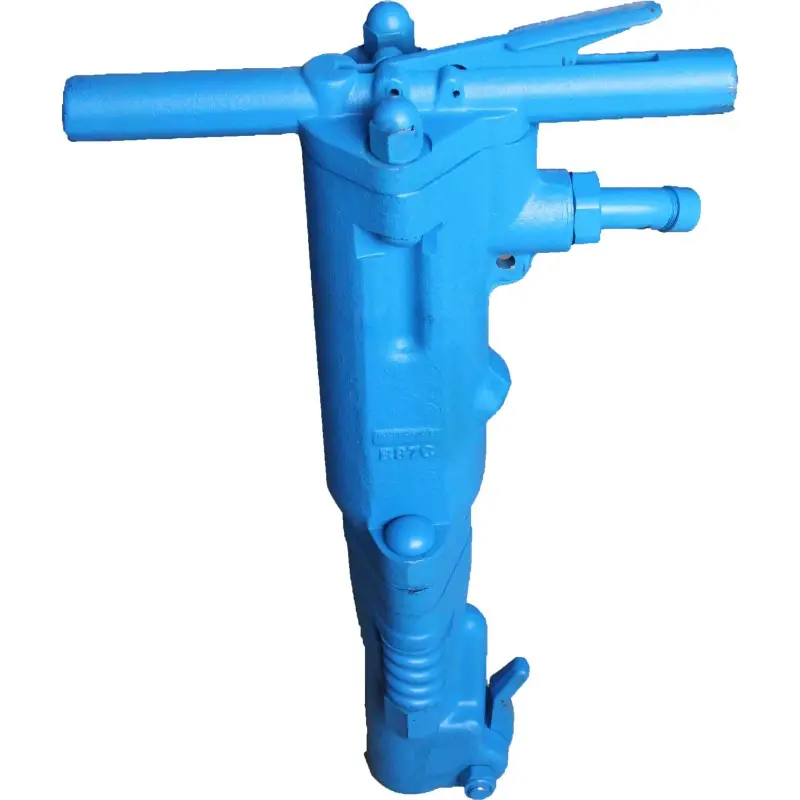
ضربات دقيقة في الهياكل المعقدة
يعد إتقان الأمور أمراً بالغ الأهمية أثناء أعمال الهدم، خاصة في المناطق القريبة من البنية التحتية المهمة. تتميز المعدات المدمجة بأنها تتيح للعمال استهداف الأماكن بدقة أكبر مقارنة بالماكينات الأكبر حجمًا، حيث توفر تحكماً ودقة لا تُضاهى. وعند تنفيذ هدم الهياكل المعقدة فعليًا، تُحدث هذه الدقة الفرق من حيث السلامة وإتمام المهمة بالشكل الصحيح. ويُثبت الخبراء في الحياة الواقعية هذه الفكرة. فعلى سبيل المثال، في مصنع إنتاج قديم مؤخرًا، واجه الفريق صعوبات في التخلص من بعض المعدات القديمة دون إحداث تلفيات. حاولوا في البداية استخدام المعدات ذات الحجم القياسي، لكنهم واجهوا مشكلات متكررة لأن تلك الماكينات الكبيرة لم تكن قادرة على التحرك بفعالية ضمن المساحات الضيقة. لكن الحل جاء عند الانتقال إلى المعدات المدمجة. فقدرت تلك الوحدات الصغيرة على المرور عبر الفتحات الضيقة واستهداف الأجزاء المراد إزالتها بدقة دون تعريض المكونات المحيطة لأي خطر.
الخصائص الأمنية المُضمنة في الكسارات الصغيرة تجعلها في الواقع أكثر كفاءة في أداء مهامها. خذ على سبيل المثال أنظمة التحكم في الاهتزاز، إلى جانب المقابض المصممة خصيصًا التي تسمح للعمال بالحفاظ على الدقة حتى أثناء العمل بالقرب من الأشخاص والمباني. هذا الأمر مهم جدًا في الأماكن الضيقة التي تكثر فيها الأنشطة المحيطة. تعمل هذه الآلات بشكل أفضل تحت الضغط دون التسبب في أضرار عرضية للمباني المحيطة. وقد وجد المقاولون أن هذه التحسينات مفيدة للغاية أثناء تنفيذ مشاريع هدم صعبة في المناطق الحضرية، حيث يجب الحفاظ باستمرار على معايير السلامة وكفاءة موقع العمل.
توافق متعدد الحاملات وكفاءة التكلفة
أنظمة تركيب بتغيير سريع
يُعد القدرة على العمل مع عدة ناقلات واحدة من أبرز الميزات المفيدة في أدوات الهدم الحديثة، حيث تتيح للعمال الانتقال بسلاسة من نوع ناقل إلى آخر في الموقع. وتجعل الأنظمة السريعة لتغيير التركيب هذا ممكنًا من خلال السماح بتغييرات سريعة في الإرفاق، مما يقلل من الوقت الضائع أثناء التحولات. وتتحول التوفير في الوقت إلى توفير في الأموال مباشرة، حيث تقلل هذه الأنظمة بشكل كبير من وقت التوقف عند التبديل بين الأدوات المختلفة. غالبًا ما تلاحظ الشركات الإنشائية التي تتبنى هذه التكنولوجيا تحسنًا في سير العمل عبر مواقعها، مما يسمح بإتمام المشاريع بشكل أسرع مع الحفاظ على إنتاجية الفرق طوال اليوم. ويُشير كثير من العاملين في الصناعة إلى التطورات التكنولوجية الحديثة في هذا المجال باعتبارها العامل الحقيقي الذي يعيد تشكيل طريقة عمل معدات الهدم اليوم، مما يمنح المقاولين المرونة اللازمة في المواقع التي يمكن أن تتغير ظروفها بسرعة من الصباح حتى المساء.
استهلاك أقل للوقود مقارنة بالبدائل الهيدروليكية
تقدم المضارب الهوائية مثل سلسلة Atlas Copco RTEX مزايا واضحة مقارنة بالبدائل الهيدروليكية، خاصة من حيث استهلاك الوقود. تُظهر الاختبارات في العالم الواقعي أن هذه الأدوات الهوائية تستهلك فعليًا حوالي نصف الهواء المضغوط الذي تستهلكه النماذج القياسية للمضارب. هذا الكفاءة الناتجة تعني توفيرًا كبيرًا في تكاليف الوقود، مما يقلل من المصروفات التشغيلية اليومية كما يسهم في تقليل الأثر البيئي. عادةً ما يؤدي التحول إلى المضارب الهوائية إلى خفض الانبعاثات الكربونية بشكل ملحوظ أثناء أعمال الهدم. وتؤكد التقارير الصناعية ذلك أيضًا، مشيرة إلى أن الشركات تلاحظ غالبًا عوائد سريعة على الاستثمار من خلال خفض التكاليف الفورية بالإضافة إلى الفوائد البيئية المستمرة. بالنسبة للشركات الإنشائية التي تسعى لجعل عملياتها أكثر صداقة للبيئة دون التأثير على الأداء المالي، تمثل الأنظمة الهوائية حلاً ذكياً يعمل بشكل جيد في الممارسة العملية.
الأسئلة الشائعة
ما هي المزايا التي تقدمها غرف الضغط الثابتة في المطارق الهوائية؟
توفر غرف الضغط الثابتة توصيل طاقة مستمر، وتُحسّن ديناميكيات تدفق الهواء، وتعزز المتانة وتقلل من تكاليف التشغيل عن طريق تقليل استخدام الهواء.
كيف تفيد أنظمة التأثير العالي عمليات الهدم؟
توفّر الأنظمة ذات التردد العالي مكاسب إنتاجية كبيرة، وتقلل من ارتداء المشغل، وهي متعددة الاستخدام بما يكفي لمعالجة مجموعة متنوعة من المواد والهياكل.
ما هي استراتيجيات تقليل استهلاك الهواء في أدوات الهدم؟
يمكن للتكنولوجيا المبتكرة لتحكم الهواء أن تؤدي إلى تقليل يصل إلى 30٪ في استخدام الهواء، مما يؤدي إلى الاستدامة البيئية ووفر التكاليف.
كيف تزيد العمليات الثنائية للأدوات من إنتاجية الهدم؟
تتيح مجموعات الأدوات الثنائية تشغيل كسور هوائية متعددة من ضاغط واحد، مما يُحسّن تخصيص الموارد ويزيد الإنتاجية.
ما هي التطورات في مجال الراحة الوظيفية التي تظهر في المضارب الهوائية؟
تشمل التطورات مقابض مخففة للارتجاج لتقليل التعب وبناء خفيف الوزن يقلل من الإجهاد البدني.
ما الفوائد التي توفرها الكسارات المدمجة في مهام الهدم الحضري؟
تُحسّن الكسارات المدمجة القدرة على المناورة في البيئات الحضرية الضيقة وتقدم ضربات دقيقة، وهي أمر حيوي للعمل بالقرب من البنية التحتية الحساسة.
لماذا اختيار الكسارات الهوائية على بدائل الهيدروليكية؟
تستهلك الكسارات الهوائية، مثل نماذج RTEX من Atlas Copco، كمية أقل من الهواء وتقدم وفورات كبيرة في الوقود، مما يعزز الاستدامة البيئية.