Rodzaje kopania Główki wiertnicze i wpływ na wydajność
Wirnikowe vs. Bity młotkowe DTH: Porównanie wskaźników przenikania
Gdy chodzi o wiercenie w operacjach górniczych, zrozumienie rodzajów główki wiertnicze mogą znacząco wpływać na wydajność. Bity obrotowe są często używane do formacji z miękkimi skałami, ponieważ wiercą przez obracanie narzędzia cięcia po powierzchni skalnej. Z drugiej strony, bity DTH (Down-The-Hole) działają za pomocą pneumatycznego młota, co czyni je odpowiednimi dla trudniejszych formacji skalnych dzięki ich uderzeniom. W kwestii szybkości przenikania, bity DTH ogólne osiągają lepsze wyniki niż bity obrotowe w trudniejszych formacjach geologicznych. Na przykład, udokumentowano, że w warunkach trudnych skał, bity DTH osiągają do 50% większą szybkość przenikania niż bity obrotowe, w zależności od twardości i kruchości materiału.
Wiele czynników wpływa na wskaźniki przenikania, w tym twardość skał, projekt ostrza i dostępność wody podczas procesu wiercenia. Jeśli skała jest twardsza, wymaga to z natury bardziej wydajnego i efektywnego sprzętu do wiercenia, takiego jak bity DTH hammer. W międzyczasie, aspekt ekonomiczny jest kluczowy dla firm przy wybieraniu między bitami wirującymi a bitami DTH. Bity DTH hammer, mimo że często kojarzą się z wyższymi początkowymi kosztami, mogą obniżyć koszty operacyjne w dłuższej perspektywie dzięki zwiększonemu wskaźnikowi przenikania i trwałości, co czyni je bardziej ekonomicznie efektywnymi w niektórych kontekstach.
Bity PDC vs. Tungsten Carbide: Wydajność zależna od zastosowania
Bity PDC (Polycrystalline Diamond Compact) i bity z karbodu wolframu są kluczowymi narzędziami w górnictwie, każda z unikalnymi właściwościami i zastosowaniami. Bity PDC składają się z cząsteczek diamentu osadzonych na podłożu, znane są ze swojej wytrzymałości i zdolności do utrzymania ostrza dłużej niż inne materiały. Bity z karbodu wolframu, tworzone z wolframu i węgla, słyną z ich odporności i mogą wytrzymać wysokie temperatury, co sprawia, że są skuteczne w zastosowaniach specjalistycznych.
Pod względem wydajności, bity PDC wyróżniają się w formacjach średnio-twardych, zapewniając długotrwałe, efektywne wiercenie z mniejszą liczbą wymian bitów. Na przykład, bity PDC mogą wykonywać wiercenia o około 20% dłuższej żywotności w porównaniu do bitów z tlenku wolframu, co ostatecznie obniża koszt na stopę wierceniową. Ta efektywność sprawia, że są wysoko cenione w sektorach naftowych i gazu. Jednakże, bity z tlenku wolframu są lepszym wyborem dla formacji skalnych dzięki swojej odporności. W przypadku ogólnej trwałości i konserwacji, bity PDC wymagają mniej częstego utrzymania, czyniąc je ekonomicznym rozwiązaniem dla długoterminowych projektów, gdzie minimalizacja simplyfikacji jest kluczowa.
Bity Przeciągowe w Miękkich Formacjach: Zrównoważenie Szybkości i Dokładności
Bity ciągnione, zaprojektowane specjalnie do wiercenia w miękkich formacjach, odgrywają kluczową rolę w utrzymaniu równowagi między szybkością a precyzją. Charakteryzujące się prostym projektem narzędzia cięcia bez ruchomych części, te bity pozwalają na szybkie przenikanie w warunkach z mniejszym oporem. To czyni bity ciągnione szczególnie skutecznymi w obszarach bogatych w glinę lub piasek, gdzie możliwa jest szybka postępka bez rezygnacji z kontroli.
Główną zaletą bity ciągnionej jest jej zdolność do zapewnienia wyższej prędkości w operacjach, gdzie precyzja pozostaje konieczna. W miękkich formacjach bity ciągnione mogą osiągnąć zyski na efektywności do 30% pod względem prędkości, nie rezygnując z dokładności cięcia. Istnieją jednak potencjalne wady. Bity ciągnione, mimo że są kosztowe, mogą szybciej się zużywać niż bardziej odporne bity stosowane w twardszych materiałach, co prowadzi do większych kosztów materiałów i zużycia operacyjnego w czasie. Mimo tych ograniczeń, bity ciągnione są godnym rozważenia rozwiązaniem dla operacji, gdzie prędkość ma pierwszeństwo przed lekko wyższą częstotliwością konserwacji, oferując równowagę w odpowiednich środowiskach.
Innowacje technologiczne zwiększające wydajność wiertniczą
Kierowana sztuczną inteligencją predykcyjna konserwacja do redukcji simplyfikacji
Napędzane sztuczną inteligencją przewidywane konserwacje to rewolucyjne podejście w operacjach wiertniczych, wykorzystujące różne technologie do przewidywania i eliminacji awarii urządzeń przed ich wystąpieniem. Dzięki wdrożeniu algorytmów SI, czujników i analizy danych, te systemy monitorują kluczowe komponenty i interpretują dane w celu przewidywania potrzeb konserwacyjnych, co znacząco obniża czas simplyfikacji. Integracja tych technologii w środowiskach przemysłowych, zwłaszcza w ramach działalności górniczej, spowodowała statystyczne poprawy, gdzie czas simplyfikacji został zmniejszony o do 30%. Takie postępy zostały pomyślnie zaimplementowane przez firmy, takie jak Komatsu, prezentując istotne ulepszenia efektywności operacyjnej. Te systemy nie tylko minimalizują niespodziewane awarie sprzętu, ale również optymalizują harmonogramy konserwacji, co przedłuża żywotność sprzętu i obniża koszty.
Automatyczne Systemy Wiertnicze i Monitorowanie Wydajności w Czasie Rzeczywistym
Automatyczne systemy wiertnicze rewolucjonizują wydajność na miejscu poprzez wykorzystanie zaawansowanych technologii do operacji wiertniczych z minimalnym udziałem człowieka. Te systemy korzystają z sztucznej inteligencji i czujników włączonych w IoT, aby ciągle monitorować i dostosowywać parametry wiercenia, co prowadzi do zwiększonej produktywności i zmniejszenia błędów. Monitorowanie wydajności w czasie rzeczywistym pozwala na natychmiastowe korekty decyzji, znacząco zwiększając precyzję wiercenia. Studium przypadku wskazuje wzrost produktywności o ponad 20% na placówkach wykorzystujących taką automatyzację. Z początkowym inwestycją w technologię, przedsiębiorstwa korzystają długoterminowo dzięki obniżonym kosztom pracy i poprawionym efektywnościom operacyjnym, prezentując przekonujący argument na rzecz inwestycji w automatyzację mimo potencjalnych początkowych kosztów.
Bity z Diamentowym Wzorcem do Dłuższego Czasu Życia Narzędzia
Projekty bity z wzmocnieniem diamentowym reprezentują istotne osiągnięcie inżynierskie, oferując znaczące korzyści pod względem trwałości i wydajności narzędzi. Te bity wykorzystują syntetyczne diamenty i zaawansowane pokrycia, ograniczając zużycie i znacznie przedłużając żywotność narzędzi w porównaniu do tradycyjnych materiałów. Kwantytyczne oceny wskazują, że bity diamentowe prezentują o do 50% niższe tempo zużycia, umożliwiając dłuższe okresy eksploatacji i zmniejszając częstotliwość wymiany. W zastosowaniach takich jak wiertnictwo geotermiczne i eksploracja kopalń, bity diamentowe zdecydowanie zwiększyły wskaźniki produkcji, poprawiając zdolność firm do spełnienia wymagających celów operacyjnych. Ta technologia ma szansę na rozwój rynku, awansując produkcję bitów wiertniczych dzięki nowoczesnym technologiom diamentowym.
Legity wolframu: Odporność na zużycie w agresywnych środowiskach
Tungsten carbide jest kluczowym materiałem w produkcji głowic wiertniczych dzięki wyjątkowej oporności na zużycie i trwałości. Jego właściwości, takie jak twardość i wytrzymałość, czynią go idealnym rozwiązaniem dla ciężkich zastosowań górniczych, gdzie długość życia jest kluczowa. W różnych warunkach górniczych wkłady z tungsten carbide w głowicach wiertniczych systematycznie przewyższały wydajność tradycyjnych materiałów. Na przykład, badania wykazały, że te wkłady mogą skutecznie radzić sobie z dużą abrazyjnością środowisk górniczych, co przedłuża żywotność narzędzi (Element Six, 2024). Jednak wybór tungsten carbide wymaga uwzględnienia równowagi między kosztem a wydajnością. Choć początkowy koszt jest wyższy niż w przypadku innych materiałów, jego długotrwałość i zmniejszone potrzeby konserwacji często usprawiedliwiają inwestycję.
W przyszłości istnieje znaczne zainteresowanie rozwijaniem zaawansowanych stopów tungalowu w celu dalszego poprawienia wydajności. Badacze badają modyfikacje w składach stopów, aby poprawić oporność na ekstremalne warunki górnicze, co sprawi, że te materiały będą jeszcze bardziej kosztodajne z czasem. W miarę jak przemysł górniczy kontynuuje swoje rozwojowe zmiany, oczekujemy wprowadzenia nowych sformułowań tungalowu, które posuną granice trwałości i efektywności wierteł.
Sztuczne noże diamentowe: Rewolucjonizacja wiercenia w twardej skale
Produkcja sztucznych nożników diamentowych obejmuje zaawansowane procesy tworzenia diamentów za pomocą technologii wysokiego ciśnienia i wysokiej temperatury (HPHT). Znane dzięki swojej wyjątkowej twardości i termicznej stabilności, sztuczne diamenty zrewolucjonizowały wiertenie twardych skał, znacząco podnosząc efektywność. Te nożniki zapewniają wybitną wydajność, jak świadczą o tym wskaźniki wskazujące na do 50% szybsze przenikanie twardych skał w porównaniu do tradycyjnych głowic wiertniczych. Ta efektywność ma istotne implikacje dla sektora górniczego, w tym zmniejszoną liczbę przestojów i zwiększoną produktywność operacyjną.
Postępy w technologii syntetycznych diamentów trwają, a ich potencjał dla przemysłu górniczego jest znaczny. Innowacje w składach macierzy i technikach łączenia otwierają drogę do bardziej wytrzymalnych i kosztowniejszych narzędzi diamentowych. Warto zauważyć, że różne operacje górnicze, które przyjęły bity z syntetycznych diamentów, zgłaszają istotne poprawy w swoich procesach wiertniczych, prezentując zarówno korzyści na krótki, jak i długoterminowe. W miarę wzrostu popytu na rozwiązania wiertnicze o wysokiej wydajności, włączanie syntetycznych diamentów ma stać się standardową praktyką w zastosowaniach w skałach twardej.
Złożone materiały do oporu na uderzenia i długowieczność
Materiały złożone osiągnęły istotny postęp w produkcji wierteł, oferując zwiększoną odporność na uderzenia oraz dłuższy okres użytkowania. Te materiały, często składające się z włókien o wysokiej sile i żywic, działają wzajemnie, aby pochłaniać energię uderzeń i zmniejszać zużycie. W szczególności, materiały złożone wykazały lepsze wyniki niż tradycyjna stal w zastosowaniach wymagających stałej niezawodności w warunkach dużego obciążenia.
Statystyki branżowe wskazują, że bursztyny złożowe mają dłuższy okres użytkowania w porównaniu do tradycyjnych bursztynów, często przedłużając czas użytkowania o 30% lub więcej. Ta trwałość oznacza mniej wymian i potrzeb konserwacji, co przekłada się na lepszą efektywność kosztową w czasie. Mimo tych zalet, nadal istnieją wyzwania związane z powszechnym wprowadzeniem materiałów złożowych, zwłaszcza w dostosowywaniu istniejących procesów produkcyjnych do nowych materiałów. Gdy te przeszkody zostaną pokonane, możemy spodziewać się, że materiały złożowe będą odgrywać coraz bardziej kluczową rolę w przyszłości technologii trwałych bursztynów, oferując solidne rozwiązania w różnych środowiskach wiertniczych.
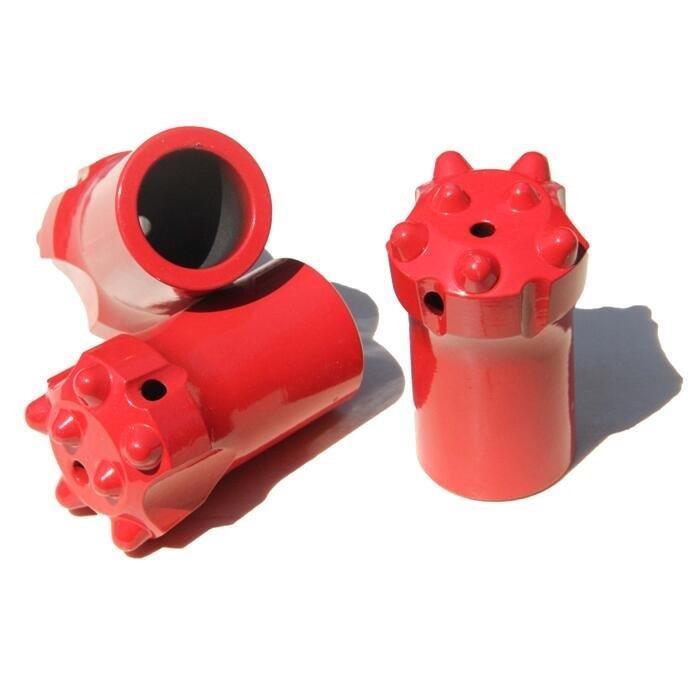
Optymalizacja wyboru bursztyna i parametrów operacyjnych
Uwagi geologiczne dotyczące efektywnego dopasowania bursztyna
Wybór odpowiedniego wiertełka jest kluczowy w optymalizacji operacji wiertniczych, a zrozumienie budowy geologicznej stanowi serce tego procesu. Każda formacja geologiczna – czy to miękka glina, gęsta sława, czy abrazyjny piaskowiec – prezentuje unikalne cechy, które mogą znacząco wpływać na wydajność wiertełka. Ekspertów rekomendacje sugerują przeprowadzenie kompleksowych ocen geologicznych za pomocą metod takich jak pobieranie rdzeni i badania sejsmiczne, aby poprawić wybór wiertełka. Na przykład, niewłaściwe połączenie wiertełek z twardej skały prowadziło do zwiększonego zużycia i obniżenia efektywności w niektórych badaniach przypadkowych. Przez dokładne badanie tych warunków formowania, operatorzy mogą się upewnić, że używają najefektywniejszych wiertełek, co kończy się zoptymalizowanymi operacjami i obniżonymi kosztami.
Optymalizacja Ciężaru na Wiertełku dla Efektywności Energetycznej
Ciężar na bicie (WOB) jest podstawą wydajności wiercenia, wpływając zarówno na zużycie energii, jak i czas życia sprzętu. Ten parametr określa siłę zastosowaną do głowicy wiertniczej, bezpośrednio wpływa na tempo przenikania (ROP). Optymalizując WOB, operatorzy mogą zmniejszyć zbędne zużycie energii i przedłużyć żywotność głowicy. Statystyki wskazują, że zoptymalizowany WOB może prowadzić do znaczącego spadku zużycia paliwa—czasami nawet o 10%. W celu praktycznej optymalizacji, operatorom zaleca się blisko monitorować dane w czasie rzeczywistym i dostosowywać WOB w oparciu o warunki wiercenia i informacje zwrotne od sprzętu, zapewniając równowagę między szybkim postępem a oszczędnościowymi operacjami energetycznymi.
Zrównoważony rozwój i kosztowna efektywność w ekstrakcji surowców mineralnych
Wskaźniki zużycia energii na metr wiercony
Rozumienie wskaźników zużycia energii w operacjach wiertniczych jest kluczowe dla promowania zrównoważonego rozwoju i efektywności. Te wskaźniki dostarczają wglądu w zapotrzebowanie na energię związane z różnymi technikami i narzędziami wiertniczymi, pomagając operatorom w identyfikacji bardziej zrównoważonych praktyk. Zgodnie z danymi branżowymi, tempo zużycia energii może znacznie się różnić między różnymi rodzajami głowic wiertniczych i warunkami geologicznymi. Na przykład, głowice diamentowe są często preferowane ze względu na swoją wydajność, co redukuje zużycie energii w porównaniu do tradycyjnych głowic. Aby zmniejszyć zużycie energii jednocześnie utrzymując skuteczność operacyjną, stosuje się strategie takie jak optymalizacja parametrów wiercenia i wykorzystywanie zaawansowanych projektów głowic. Obecne trendy branżowe przesuwają się w kierunku bardziej oszczędzających energię rozwiązań wiertniczych, napędzane rosnącymi regulacjami i globalnymi celami zrównoważonego rozwoju.
Analiza kosztów cyklu życia premium versus standardowych głowic
Analiza kosztów cyklu życia (LCA) jest kluczowym narzędziem do oceny całkowitych kosztów posiadania wiertnic w ciągu ich żywota, oferując wgląd w zakup i planowanie finansowe. Wierte premium, mimo wyższych początkowych kosztów, często zapewniają lepszą wydajność i dłuższą żywotność, co redukuje ogólne koszty w długotrwałych operacjach. Dane porównawcze pokazują, że wierte premium, które zazwyczaj mają wbudowane zaawansowane technologie, generują wyższą efektywność i zmniejszają czas przestoju w porównaniu do standardowych wirtek. Na przykład, wierte premium mogą znacząco obniżyć koszty konserwacji i zwiększyć produktywność w surowych warunkach wiertniczych. Użycie LCA pomaga operatorom podejmować świadome decyzje, pokazując, jak inwestycja w opcje premium może prowadzić do istotnych korzyści finansowych poprzez minimalizację długoterminowych wydatków i zwiększenie efektywności. Studia przypadków częstokroć podkreślają sukces firm, które przyjęły wirte premium, prezentując ich finansowe zalety dzięki zmniejszeniu przerw w operacjach i utrzymaniu wydajności.
Sekcja FAQ
Jaka jest różnica między wiertłami obrotowymi a wiertłami DTH (Down-The-Hole)?
Wiertła obrotowe są wykorzystywane do formacji skalnych miększych i działają przez obracanie narzędzia cięcia po powierzchni skały. Wiertła DTH działają przy użyciu pneumatycznego młota i są odpowiednie do zastosowania w formacjach skalnych twardszych dzięki ich percusyjnej akcji.
Dlaczego wiertła PDC są woli preferowane niż wiertła z karbidy wolframu dla formacji średnio-twardych?
Wiertła PDC mają cząsteczki diamentu osadzone na podłożu, co sprawia, że są odporne i dłużej zachowują ostry krawędź, zapewniając efektywne wielenie z mniejszą liczbą wymian wiertła w porównaniu do wiertł z karbidy wolframu.
Jak wiertła przesuwne poprawiają wielenie w formacjach miękkich?
Wiertła przesuwne są projektowane do szybkiego przenikania w formacjach miękkich z mniejszym oporem, oferując zyski w zakresie szybkości bez rezygnacji z dokładności cięcia.
Jak systemy predykcyjnego konserwowania sterowane sztuczną inteligencją korzystają operacjom wielenia?
Te systemy używają algorytmów sztucznej inteligencji i czujników do przewidywania i eliminowania awarii equipment przed ich wystąpieniem, co redukuje simplyfikację i optymalizuje harmonogramy konserwacji.
Jakie korzyści oferują konstrukcje bitych wzmocnionych diamentem?
Bity wzmocnione diamentem oferują niższe tempo zużycia oraz dłuższy okres użytkowania narzędzia, co poprawia wskaźniki produkcji i zmniejsza częstotliwość wymiany.