Types of Mining Drill Bits and Efficiency Impact
Rotary vs. DTH Hammer Bits: Comparing Penetration Rates
When it comes to drilling in mining operations, understanding the types of drill bits can significantly affect efficiency. Rotary bits are often used for softer rock formations as they drill by rotating a cutting tool against the rock surface. On the other hand, DTH (Down-The-Hole) hammer bits operate with a pneumatic hammer, making them suitable for harder rock formations due to their percussive action. In terms of penetration rates, DTH hammer bits generally outperform rotary bits in harder geological formations. For instance, it has been documented that in tough rock conditions, DTH hammer bits achieve up to 50% higher penetration rates than rotary bits, depending on the hardness and brittleness of the material.
Several factors impact penetration rates, including rock hardness, bit design, and water availability during the drilling process. If the rock is harder, it inherently requires more robust and efficient drilling equipment, like DTH hammer bits. Meanwhile, the economic aspect is crucial for businesses when choosing between rotary and DTH bits. DTH hammer bits, although often associated with higher initial costs, may reduce operational costs in the long run due to increased penetration rates and durability, making them more economically efficient in certain contexts.
PDC Bits vs. Tungsten Carbide: Application-Specific Performance
PDC (Polycrystalline Diamond Compact) bits and tungsten carbide bits are essential tools in mining, each with unique attributes and applications. PDC bits comprise diamond particles embedded on a substrate, known for their resilience and ability to maintain a sharp edge longer than other materials. Tungsten carbide bits, formed from tungsten and carbon, are renowned for their toughness and can endure high temperatures, making them effective in specialized applications.
In terms of performance, PDC bits excel in medium-hard formations, delivering long-lasting, efficient drilling with fewer bit replacements. For example, PDC bits can complete drills with about 20% longer lifespan compared to tungsten carbide bits, ultimately reducing the cost-per-foot drilled. This efficiency makes them highly valued in petroleum and gas sectors. However, tungsten carbide bits are preferable for hard rock formations due to their toughness. When it comes to overall longevity and maintenance, PDC bits require less frequent maintenance, making them a cost-effective choice for prolonged projects where minimizing downtime is vital.
Drag Bits in Soft Formations: Balancing Speed and Precision
Drag bits, designed explicitly for drilling in soft formations, play a pivotal role in maintaining a balance between speed and precision. Characterized by their simple cutting tool design with no moving parts, these bits allow fast penetration in conditions with less resistance. This makes drag bits particularly effective in clay-rich or sandy areas where quick advancement is possible without compromising on control.
The primary advantage of drag bits is their ability to provide superior speed in operations where precision remains necessary. In soft formations, drag bits can achieve efficiency gains up to 30% in terms of speed without sacrificing the accuracy of the cut. However, there are potential drawbacks. Drag bits, while cost-effective, may wear faster than more robust bits used in harder materials, leading to higher material costs and operational wear over time. Despite these limitations, drag bits are a worthwhile consideration for operations where speed outweighs the slightly higher maintenance frequency, providing a balanced solution in suitable environments.
Technological Innovations Enhancing Drilling Efficiency
AI-Driven Predictive Maintenance for Downtime Reduction
AI-driven predictive maintenance is a transformative approach in drilling operations, utilizing various technologies to anticipate and address equipment failures before they occur. By deploying AI algorithms, sensors, and data analytics, these systems monitor critical components and interpret data to predict maintenance needs, drastically reducing downtime. The integration of these technologies in industrial settings, notably within mining operations, has led to statistical improvements where downtime has been reduced by up to 30%. Such advancements have been successfully implemented by companies like Komatsu, showcasing significant operational efficiency enhancements. These systems not only minimize unexpected equipment malfunctions but also optimize maintenance schedules, thereby extending equipment life and lowering costs.
Automated Drilling Systems and Real-Time Performance Monitoring
Automated drilling systems are revolutionizing on-site efficiency by leveraging advanced technologies for drilling operations with minimal human intervention. These systems use AI and IoT-enabled sensors to continuously monitor and adjust drilling parameters, leading to enhanced productivity and error reduction. Real-time performance monitoring allows immediate decision-making adjustments, significantly increasing drilling precision. A case study highlights a productivity surge of over 20% in sites utilizing such automation. With the initial investment in technology, businesses benefit long-term through reduced labor costs and improved operational efficiencies, presenting a compelling case for investing in automation despite potential upfront expenses.
Diamond-Enhanced Bit Designs for Extended Tool Life
Diamond-enhanced bit designs represent a notable engineering breakthrough, offering significant advantages in tool durability and performance. These bits employ synthetic diamonds and advanced coatings, curtailing wear rates and prolonging tool life substantially compared to traditional materials. Quantitative assessments reveal that diamond bits exhibit up to 50% lower wear rates, facilitating prolonged operational periods and decreasing replacement frequency. In applications like geothermal drilling and mining exploration, diamond bits have demonstrably boosted production rates, enhancing companies' ability to meet demanding operational goals. This technology is poised for market expansion, advancing drill bit manufacturing with emerging diamond technologies.
Tungsten Carbide Alloys: Wear Resistance in Abrasive Environments
Tungsten carbide is a critical material in drill bit manufacturing due to its exceptional wear resistance and durability. Its properties, such as hardness and toughness, make it ideal for heavy-duty mining applications where longevity is paramount. In various mining settings, tungsten carbide inserts in drill bits have consistently exceeded the performance of conventional materials. For example, studies have shown that these inserts can handle the heavy abrasiveness of mining environments effectively, thereby extending the lifespan of tools (Element Six, 2024). However, selecting tungsten carbide involves considering the balance between cost and performance. While its initial cost is higher than other materials, its longevity and reduced maintenance needs often justify the investment.
Looking ahead, there is considerable interest in developing advanced tungsten carbide alloys to further enhance performance. Researchers are exploring adjustments in alloy compositions to improve resistance to extreme mining conditions, which would make these materials even more cost-effective over time. As the mining industry continues to evolve, we anticipate the introduction of new tungsten carbide formulations that will push the boundaries of drill bit durability and efficiency.
Synthetic Diamond Cutters: Revolutionizing Hard Rock Drilling
The production of synthetic diamond cutters involves sophisticated processes that create diamonds using high-pressure, high-temperature (HPHT) technology. Known for their unmatched hardness and thermal stability, synthetic diamonds have revolutionized hard rock drilling by significantly enhancing efficiency. These cutters provide excellent performance, as evidenced by metrics indicating up to 50% faster penetration rates in hard rock compared to traditional drill bits. This efficiency has major implications for the mining sector, including reduced downtime and increased operational productivity.
Advancements in synthetic diamond technology are ongoing, and their potential for the mining industry is substantial. Innovations in matrix compositions and bonding techniques are paving the way for more resilient and cost-effective diamond tools. Notably, various mining operations that have adopted synthetic diamond bits report substantial improvements in their drilling processes, showcasing both short-term and long-term benefits. As the demand for high-performance drilling solutions grows, incorporating synthetic diamonds is set to become a standard practice in hard rock applications.
Composite Materials for Impact Resistance and Longevity
Composite materials have made significant strides in drill bit manufacturing, offering enhanced impact resistance and longevity. These materials, often composed of high-strength fibers and resins, work synergistically to absorb impact energy and reduce wear. In particular, composites have outperformed traditional steel in applications requiring consistent reliability under high-stress conditions.
Industry statistics illustrate that composite drill bits experience a longer operational life compared to conventional bits, often extending service life by 30% or more. This longevity translates into fewer replacements and maintenance needs, contributing to better cost efficiency over time. Despite these advantages, challenges remain in the widespread adoption of composites, particularly in adapting existing manufacturing processes to accommodate new materials. As these hurdles are overcome, we can expect composites to play an increasingly pivotal role in the future of durable drill bit technology, providing robust solutions across various drilling environments.
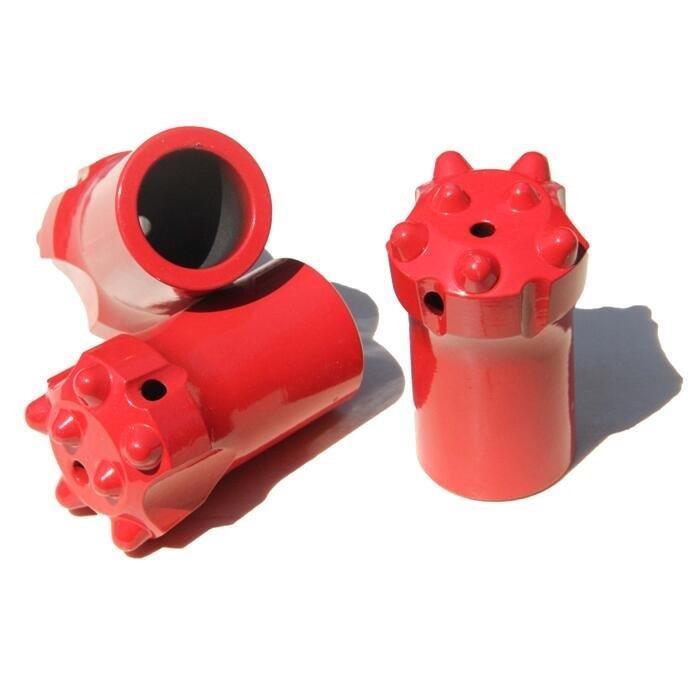
Optimizing Bit Selection and Operational Parameters
Geological Considerations for Effective Bit Matching
The selection of the right drill bit is crucial in optimizing drilling operations, and understanding geological formations is at the heart of this process. Every geological formation—be it soft clay, dense shale, or abrasive sandstone—presents unique characteristics that can significantly impact drill bit performance. Expert recommendations suggest conducting comprehensive geological assessments using methods like core sampling and seismic surveys to enhance bit selection. For instance, the inappropriate pairing of drill bits with hard rock formations has led to increased wear and reduced efficiency in some case studies. By closely examining these forming conditions, operators can ensure they use the most effective bits, ultimately leading to streamlined operations and reduced costs.
Weight-on-Bit Optimization for Energy Efficiency
Weight-on-bit (WOB) is fundamental to drilling efficiency, impacting both energy consumption and equipment lifespan. This parameter determines the force applied to the drill bit, directly affecting the rate of penetration (ROP). By optimizing WOB, operators can reduce unnecessary energy expenditure and prolong bit life. Statistics reveal that optimized WOB can lead to a notable reduction in fuel consumption—sometimes by as much as 10%. For practical optimization, operators are advised to monitor real-time data closely and adjust WOB based on drilling conditions and equipment feedback, ensuring a balance between rapid advancement and energy-efficient operations.
Sustainability and Cost Efficiency in Mineral Extraction
Energy Consumption Metrics per Meter Drilled
Understanding energy consumption metrics in drilling operations is crucial for promoting sustainability and efficiency. These metrics provide insights into the energy demands associated with different drilling techniques and tools, aiding operators in identifying more sustainable practices. According to industry data, energy consumption rates can vary significantly among various types of drill bits and geological conditions. For example, diamond bits are often preferred for their efficiency, reducing energy use compared to traditional bits. To minimize energy usage while maintaining operational effectiveness, strategies such as optimizing drilling parameters and leveraging advanced bit designs are employed. Current industry trends are shifting towards more energy-efficient drilling solutions, driven by increasing regulations and global sustainability goals.
Lifecycle Cost Analysis of Premium vs. Standard Bits
Lifecycle cost analysis (LCA) is a vital tool for evaluating the total cost of ownership for drill bits over their lifespan, offering insights into procurement and financial planning. Premium drill bits, though initially more expensive, often deliver superior performance and longevity, reducing overall costs in extended operations. Comparative data illustrate that premium bits, which usually have advanced technologies embedded, yield higher efficiency and reduce downtime compared to standard bits. For instance, premium bits can significantly lower maintenance costs and enhance productivity in harsh drilling environments. Using LCA helps operators make informed choices, demonstrating how investing in premium options can lead to substantial financial benefits by minimizing long-term expenses and boosting efficiency. Case studies frequently highlight the success of companies that adopted premium bits, showcasing their financial advantages through reduced operational disruptions and sustained performance.
FAQ Section
What is the difference between rotary and DTH hammer bits?
Rotary bits are used for softer rock formations and drill by rotating a cutting tool against the rock surface. DTH hammer bits operate with a pneumatic hammer and are suitable for harder rock formations due to their percussive action.
Why are PDC bits preferred over tungsten carbide for medium-hard formations?
PDC bits have diamond particles embedded on a substrate, making them resilient and they maintain a sharp edge longer, providing efficient drilling with fewer bit replacements compared to tungsten carbide bits.
How do drag bits benefit drilling in soft formations?
Drag bits are designed for fast penetration in soft formations with less resistance, offering efficiency gains in terms of speed without sacrificing cut accuracy.
How do AI-driven predictive maintenance systems benefit drilling operations?
These systems use AI algorithms and sensors to anticipate and address equipment failures before they occur, reducing downtime and optimizing maintenance schedules.
What advantages do diamond-enhanced bit designs offer?
Diamond-enhanced bits provide lower wear rates and extended tool life, enhancing production rates and decreasing replacement frequency.