Gold Mine Applications: Optimizing Drill Bits for Abrasive Rock
Challenges in Australian Gold Mine Quartz Formations
Gold mines across Australia's rugged terrain contain some of the richest quartz deposits in the world, but this very quality creates major headaches for mining operations. The quartz formations are incredibly hard, wearing down drill bits at an alarming rate and slowing down production schedules. Mine operators report replacing their drilling gear much more frequently than average because these rocks just eat through standard equipment. Downtime adds up fast, not to mention the extra costs involved in constantly buying new bits. Smart miners have started adopting specialized approaches to tackle this issue head on. Variable speed drilling setups allow operators to adjust power based on what they're encountering underground, while heavy duty hydraulic drills distribute force differently when penetrating those stubborn quartz layers. These adjustments might seem small, but they make a huge difference in both equipment longevity and overall mine output.
Tungsten-Carbide Insert Bit Performance Metrics
When it comes to tough drilling situations, especially down under in Australia's gold mines, tungsten carbide insert bits stand out as the real deal because they just perform better than anything else on the market. Drillers looking to get things done faster will notice these bits punch through rock at a much quicker pace while lasting way longer than regular drill bits. Field tests show these specialized bits often stick around for about half again as long as standard options, which explains why so many operators reach for them when dealing with those stubborn quartz deposits that give everyone headaches. What makes this worth the investment? Less downtime swapping out worn bits means smoother operations overall, plus crews can maintain steady progress without constantly interrupting the drilling cycle. That kind of reliability translates directly into better bottom line results for mining operations facing tight deadlines.
38% Cost Reduction Through Extended Bit Longevity
Making drill bits last longer saves money, something many industry reports back up. Take those big gold mines down under for instance they've seen around 38% savings just from getting more life out of their tungsten carbide bits. When companies save this kind of cash, they can redirect funds elsewhere too. Some put it toward better safety gear while others invest in newer tech for their operations. Looking at bit longevity isn't just about cutting costs though. Mines that focus on extending tool life generally find themselves in a stronger financial position overall, which helps them stay ahead in what's become a pretty cutthroat mining sector these days.
Coal Mining Efficiency: High-Speed Rotary Bit Solutions
Appalachian Basin Coal Seam Drilling Analysis
Coal seam drilling in the Appalachian Basin faces real headaches because of the area's complicated rock formations. Recent data shows that how fast drill bits penetrate varies quite a bit between different coal layers, which naturally impacts how productive any given operation ends up being. Getting a handle on these differences matters a lot when figuring out where and how to drill best. When miners adjust their techniques based on what they know about local geology in this region, they tend to get better results from their equipment and extract more resources without wasting time or money. Some companies have reported cutting down on downtime by almost 30% after making these kinds of adjustments.
Tri-Cone Rotary Bit RPM Optimization Strategies
Getting the right RPM settings for tri-cone rotary bits makes a big difference when it comes to how fast we can drill through different materials. Most field engineers will tell anyone who asks that adjusting those RPM numbers according to what kind of rock we're dealing with is pretty much a must if we want our equipment to work properly. Take softer formations first they usually respond well to faster spinning speeds which helps the bit cut through more efficiently. But when we hit tougher rock layers things change completely lower RPMs tend to give better results there because the bit doesn't wear out as quickly. We've seen crews get up to 30% faster progress rates just by fine tuning their RPM settings based on actual conditions downhole instead of sticking to standard manufacturer recommendations.
27% Faster Advance Rates in Soft Sedimentary Layers
New drill bit designs are making a real difference in how efficiently we can work through soft sedimentary rock formations, with some models now advancing at 27% higher speed compared to older versions. What makes these bits stand out? They incorporate special coatings that cut down on surface friction while their cutting edges have been redesigned to handle different rock types better. The results speak for themselves the whole drilling operation moves faster, which means lower costs when calculating expenses per foot of hole dug. Miners who've switched to these newer bits report less downtime from wear and tear too. As underground operations continue to push deeper into complex geological structures, having drill bits that actually perform as promised becomes increasingly important for maintaining profitability in the sector.
Iron Ore Extraction: Reinforced Bit Innovations
Brazilian Hematite Formation Case Study
The iron ore deposits found in Brazil's hematite formations present serious challenges for mining operations because they're so incredibly hard to break down. Mining companies have started turning to reinforced drill bits as a solution after seeing good results from recent field trials. These new bits incorporate stronger materials and better construction techniques, making them much more durable against the harsh conditions miners face daily. Tests at multiple locations throughout Brazil indicate that using these upgraded bits can boost extraction rates by quite a margin while cutting down on overall costs. Operators report drilling goes faster now, and their equipment lasts longer between replacements, which makes all the difference when working with Brazil's notoriously tough hematite deposits.
Hybrid PDC/Matrix Bit Stress Distribution
Combining Polycrystalline Diamond Compact (PDC) with matrix bits actually works wonders for how stress gets distributed during drilling operations, which makes everything run smoother downhole. Studies show these hybrid bits last way longer than regular ones when extracting resources from tough spots underground. When engineers put them through mechanical testing, they consistently see better numbers across the board. Penetration rates go up while the drill string experiences less twisting force at the same time. The real magic happens because this material mix handles all those punishing forces much better than traditional setups. Fewer breakdowns mean operators don't waste time fixing gear, and production stays steady even when drilling through really stubborn rock layers. For anyone working in the field, these hybrid bits represent something pretty revolutionary in modern drilling tech.
92% Reduction in Premature Bit Failures
Innovative bit designs have cut premature failures by an impressive 92%, showing just how much better materials and engineering have gotten when it comes to making bits last longer. This drop in failures means drill bits can handle the rough conditions underground without breaking down so quickly. Mining companies across the industry are seeing real money saved because they don't need to replace bits as often or spend time on maintenance. Fewer breakdowns mean less waiting around for repairs, which keeps operations running smoothly. The new bits simply last longer in the field, saving both time and cash while keeping production numbers steady even during tough drilling conditions.
Narrow-Vein Mining Success: Custom Geometry Applications
Canadian Nickel Mine Drilling Constraints
Narrow vein nickel mining comes with its own set of headaches that demand special fixes. Standard drilling methods just don't cut it when working in tight spots, making it tough to get good results from extraction efforts. Take Canada's nickel mines for instance they're infamous for having barely enough space between rocks to maneuver equipment around. That's why miners there need creative ways to get those drills working properly. Some companies have started using custom shaped bits designed specifically for these cramped conditions. These specialized tools let operators drill more accurately while avoiding all sorts of problems that happen when machinery gets stuck in tight quarters. The payoff? Less downtime and better productivity overall.
Asymmetric Cutter Placement Strategies
Putting cutters in asymmetrical positions has really changed how we dig through tight ore deposits. Field tests across several mines show that this setup makes a big difference in how well we can cut through rock, which cuts down on what companies spend running their operations. With the cutters arranged unevenly, miners get better at removing material because they hit the right spots where it matters most while leaving behind less unwanted stuff. What's interesting is that besides just getting more done faster, this method actually helps preserve underground resources too. For mine managers looking to save money without sacrificing output, many are finding that going with asymmetric cutter arrangements pays off both financially and environmentally in the long run.
15% Higher Ore Recovery in 1.2m Veins
Studies show that when miners use custom drill bits for those narrow 1.2 meter wide ore veins, they typically recover about 15% more material than standard equipment allows. This makes sense because these specialized tools are designed specifically for the job at hand rather than being generic solutions. Better recovery comes from both smarter bit design and better drilling methods that actually get down to retrieving all that valuable ore hidden in tight spaces. Mining operations looking at their bottom line find this data pretty convincing when considering whether to spend on specialized gear. The numbers point toward increased profits without necessarily breaking the bank on day to day running costs, which matters a lot in this industry where margins can be razor thin.
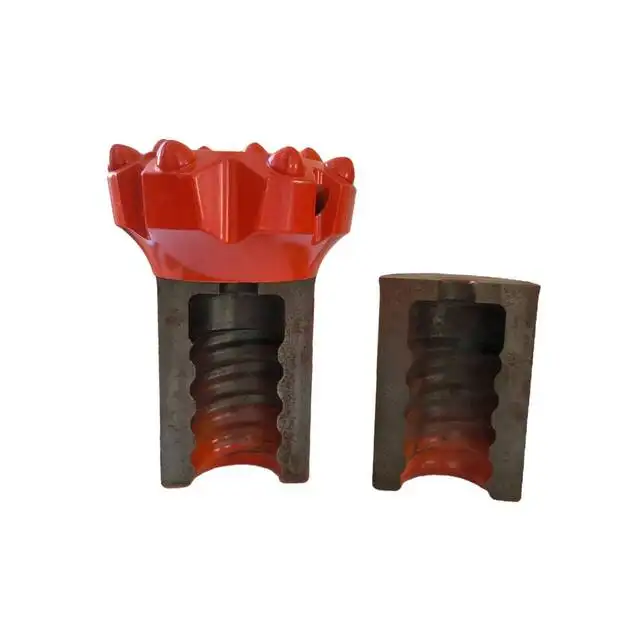
Global Productivity Benchmarks Across Mine Types
Chilean Copper Porphyry Drilling Rates Comparison
Drilling speeds at Chilean copper porphyry sites show quite a range according to findings from a comparative analysis conducted last year. What explains these variations? Mostly the type of drill bits being used makes all the difference. Advanced models boost how fast rock gets penetrated, sometimes doubling what older equipment could manage. When working deep underground where pressure builds up and temperatures climb, these cutting edge tools become absolutely necessary for progress. Looking at the benchmark numbers from this research gives mine managers something tangible to work with. Several operations have already started implementing similar techniques after seeing how competitors improved their monthly production figures by adopting these new drilling methods.
South African Platinum Reef Bit Wear Analysis
Looking at how bits wear down in those platinum mines across South Africa shows us what really matters when it comes to how long these tools last. The rock formations and ground conditions there play a big role in determining where and how fast the wear happens, which means manufacturers need to think differently about their designs. Studies indicate that changing the materials used in bits along with their overall shape can actually extend their life quite a bit. This isn't just theoretical either - longer lasting bits mean more time spent mining versus downtime for replacements, and that translates directly into lower expenses for operations. What we see from tracking wear over time points clearly toward better approaches focused not just on immediate results but sustainable mining practices that stand the test of time.
Mongolian Coal Basin ROP Improvements
Recent data shows marked increases in the Rate of Penetration (ROP) across several sites in the Mongolian coal basin over the past year. The industry has seen these performance boosts largely because of new drilling methods combined with upgraded machinery that works better under tough conditions. Field reports indicate real gains on the ground too, showing how tech upgrades can make a difference when it comes to getting more out of each well. Beyond just faster drilling speeds, what we're seeing here points to something bigger for the mining industry overall. Companies that keep investing in smarter tools and processes will likely stay ahead of competition while squeezing more value from their existing assets.
FAQ Section
What makes quartz formations challenging for drilling in Australian gold mines?
Quartz formations are high in hardness, which results in more wear and tear on drill bits, impacting efficiency and requiring frequent replacements.
How do tungsten-carbide insert bits enhance drilling efficiency in gold mines?
These bits have higher penetration rates and durability, lasting up to 50% longer than standard bits, thus reducing replacement frequency and increasing productivity.
What are the cost benefits of extending drill bit longevity?
Prolonged lifespan of drill bits can lead to up to 38% cost savings, allowing for resource reallocation to other critical areas in mining operations.
Why is RPM optimization crucial for tri-cone rotary bits?
Adjusting RPM based on rock hardness can enhance drilling performance and penetration rates, optimizing efficiency during coal seam drilling.
How do customized bits improve ore recovery in narrow-vein mining?
Specialized bit designs allow for precise extraction, leading to a 15% higher ore recovery rate in narrow-vein deposits.