Next-Generation Materials Revolutionizing Drill Bit Construction
Tungsten-Carbide Alloys and Composite Blends
In the realm of drill bit construction, tungsten-carbide alloys have emerged as frontrunners due to their exceptional durability and cutting efficiency. These alloys are renowned for their hardness, which significantly reduces wear and extends the lifespan of drill bits. Advancements in composite blends further enhance performance by combining various materials to optimize strength, ductility, and corrosion resistance. For example, newer composite blends integrate ceramics or metallic fibers, which contribute to improved thermal stability and wear resistance. Empirical data suggests these advancements have increased drilling speed by up to 30% and lifespan by nearly 50% compared to traditional materials. Such improvements are critical for high-efficiency drilling operations.
PDC Technology and Synthetic Diamond Innovations
Polycrystalline Diamond Compact (PDC) technology represents a pivotal advancement in modern drill bits, particularly for challenging environments. PDC bits utilize synthetic diamonds created through high-pressure, high-temperature processes, offering unparalleled hardness and wear resistance. These synthetic diamonds are strategically embedded into the drill bits, effectively cutting through hard rock formations with ease. According to industry experts, PDC technology outperforms conventional tools due to its ability to drill faster and endure longer in abrasive formations, making it indispensable in hard rock environments. The application of synthetic diamonds not only improves performance but also reduces operational costs by minimizing the need for frequent bit replacements.
High-Performance Steel Matrix Developments
Recent developments in high-performance steel matrices have significantly augmented drill bit resilience and toughness. Through advanced manufacturing techniques, such as powder metallurgy, these steel matrices achieve enhanced structural integrity and robustness, enabling them to withstand the rigors of demanding drilling conditions. The innovative design and material composition reduce wear rates and lengthen the lifespan of these steel bits compared to standard steel options. Empirical comparisons show that high-performance steel bits exhibit wear rates that are 20% lower, further solidifying their dominance in durable and efficient drilling solutions. This technological progress in steel matrix design continues to set new benchmarks for drill bit durability.
Mechanism of Abrasion-Active Cutting Edges
Self-sharpening drill bits revolutionize traditional drilling approaches with their unique mechanical principles. The concept hinges on abrasion-active cutting edges that maintain sharpness by progressively wearing away weaker material, revealing a fresh, sharp cutting edge beneath. This mechanism significantly reduces the time lost to downtime for sharpening or replacement, thus improving overall efficiency during drilling operations. For instance, industries employing self-sharpening designs report notable improvements in cutting efficiency. Studies in various sectors have shown these designs significantly enhance operational functionality by maintaining consistent sharpness throughout their use, resulting in more effective and uninterrupted drilling processes.
Impact on Operational Costs and Waste Reduction
The introduction of self-sharpening drill bit designs has substantially impacted operational costs and waste generation. By extending the lifecycle of the drill bits, these designs diminish the frequency of replacements, thereby lowering operational costs. This reduced need for frequent replacements also means fewer drill bits are discarded, positively impacting environmental sustainability efforts. According to industry assessments, companies using self-sharpening bits have observed substantial cost savings, as these designs lead to fewer purchases and reduced waste management expenses. Consequently, such advancements not only enhance economic efficiency but also align with sustainable drilling practices by reducing tool waste and extending their useful life, embodying a more environmentally conscious approach in the industry.
Advanced Surface Treatments for Extreme Conditions
Nanostructured Thermal Barrier Coatings
Nanostructured thermal barrier coatings play a critical role in offering thermal protection and longevity to drill bits employed in extreme conditions. These coatings are designed to withstand high temperatures and pressures, reducing wear and tear by providing an insulating barrier between the tool and the harsh environment. Technological advancements have enabled the effective application of these coatings, enhancing their adherence and durability. A study from the Journal of Coatings Technology highlights how such coatings can resist thermal cycling, improving the tool's lifespan significantly. Under extreme drilling conditions, these advanced coatings ensure that the drill bits perform optimally, minimizing equipment failures and downtime.
Abrasion-Resistant Layer Deposition Techniques
Applying abrasion-resistant layers to drill bits involves several techniques, each with distinct advantages for enhancing wear resistance. Techniques such as physical vapor deposition (PVD) and chemical vapor deposition (CVD) allow for a uniform layer of protective material to be applied, effectively shielding the drill bit from erosion. This preventive measure not only increases the longevity of the drill bits but also optimizes their performance by maintaining their sharpness over extended periods. Research conducted by the International Journal of Advanced Manufacturing Technology demonstrates how these techniques contribute significantly to prolonging drill bit life, resulting in reduced operational costs and improved efficiency. By incorporating abrasion-resistant surfaces, drill bits can withstand the demands of heavy-duty mining operations, offering sustainable solutions in mining processes.
Modular Systems and Circular Economy Applications
Interchangeable Component Design Philosophy
The concept of modular drill bit systems revolves around designing drill bits with interchangeable components. This design philosophy allows mining operations to adapt and customize equipment more efficiently, enhancing operational flexibility. **Modular systems** enable quick and easy replacement of worn-out parts, reducing downtime and maintenance costs significantly. By adopting **interchangeable components**, companies can save on replacement expenses, as individual parts can be swapped instead of discarding entire drill bits.
Examples from the industry highlight how these systems improve flexibility; for instance, certain **down-the-hole drilling** operations in the mining sector have successfully integrated modular bits to optimize performance across varying terrains. These systems not only provide cost efficiency but also cater to specific drilling requirements, embodying the essence of tailored engineering solutions. Modular components inherently promote a sustainable approach, where customization meets functionality, paving the way for resource-efficient drilling technologies.
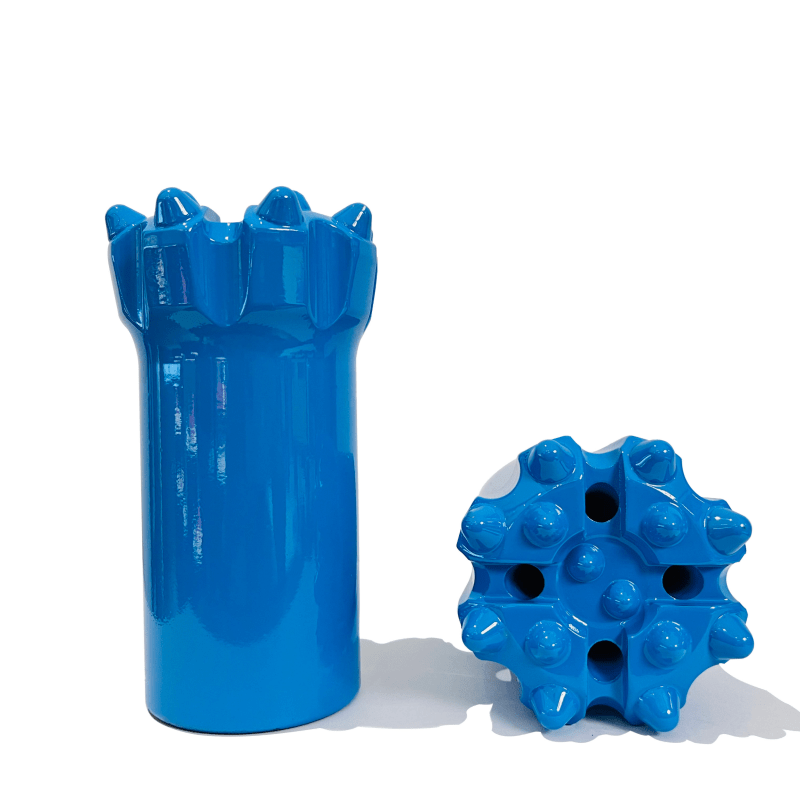
Environmental Benefits of Partial Bit Recycling
Partial recycling of drill bits presents significant environmental advantages, aligning perfectly with the principles of the **circular economy** within the mining sector. By recycling specific components of drill bits, the industry reduces waste, conserves resources, and minimizes its ecological footprint. This practice ensures that valuable materials are reintroduced into the manufacturing cycle, lessening the depletion of natural resources.
Statistical data reveals that **resource conservation** through recycling can lead to a substantial reduction in waste production. For example, reports indicate that partial bit recycling can lower material waste by up to 40%, showcasing an effective strategy in reducing environmental impact. Further, adopting such recycling methods encourages innovation in **drill bit design**, emphasizing sustainability without compromising functionality. By integrating circular economy principles, the mining industry not only enhances its ecological credentials but also drives forward-thinking practices that protect the planet for future generations.
Sustainable Mining Through Drill Bit Innovation
Reducing Energy Consumption Per Meter Drilled
Innovations in drill bit technology are pivotal in reducing energy consumption per meter drilled, thereby fostering sustainable mining practices. The development of advanced drill bits utilizing cutting-edge materials and aerodynamic designs substantially decreases resistance during drilling operations, resulting in significant energy savings. For instance, the incorporation of composite materials in drill bit manufacturing enhances durability and efficiency, leading to reduced power requirements and extended operational lifespan. Prominent experts in sustainable mining emphasize the critical role of energy-efficient practices, arguing that reducing energy consumption not only lowers operational costs but also minimizes environmental impact, aligning with broader sustainability goals. As the mining sector continues to embrace green initiatives, leveraging drill bit innovations becomes indispensable in achieving energy-efficient and environmentally conscious mineral extraction.
Supporting Low-Impact Mineral Extraction Goals
New drilling technologies play a significant role in supporting low-impact mineral extraction, embodying the principles of sustainable development in the mining industry. Advanced drill bit designs aim to minimize environmental disruption, enabling precise and efficient extraction with minimal wastage and reduced surface damage. Industry targets for sustainability are increasingly centered around environmentally friendly practices, and innovations in drilling technologies contribute to achieving these goals by offering more sustainable and less invasive extraction methods. Regulatory frameworks, such as the United Nations Sustainable Development Goals, endorse sustainable mining practices that prioritize ecological preservation and resource conservation. By adopting low-impact technologies, the mining industry can align with these frameworks and fulfill its commitment to responsible resource management, paving the way for a more sustainable future.
FAQ
What are tungsten-carbide alloys used for in drill bit construction?
Tungsten-carbide alloys are used for their exceptional durability and cutting efficiency, significantly reducing wear and extending the lifespan of drill bits.
How does PDC technology benefit drill bit performance?
PDC technology utilizes synthetic diamonds for unparalleled hardness and wear resistance, allowing drill bits to cut through hard rock formations effectively, reducing operational costs due to less frequent bit replacements.
What are the advantages of self-sharpening drill bits?
Self-sharpening drill bits maintain sharpness via abrasion-active cutting edges, reducing downtime for sharpening or replacement, thus improving overall drilling efficiency.
How do advanced surface treatments protect drill bits?
Advanced surface treatments like nanostructured thermal barrier coatings and abrasion-resistant layer deposition enhance drill bit durability and wear resistance, minimizing equipment failures in extreme drilling conditions.
What is the significance of modular drill bit systems?
Modular drill bit systems offer interchangeable components, allowing quick replacement of worn-out parts, enhancing operational flexibility and reducing maintenance costs.
How does partial bit recycling aid in environmental sustainability?
Partial recycling of drill bits conserves resources, reduces waste, and aligns with the principles of the circular economy, minimizing the mining industry's ecological footprint.